Manufacturer of Mitered Pipe Bends | ASME/ANSI B16.9, ANSI B16.28, MSS-SP-43
A mitered pipe bend is a type of pipe bend where the pipe is cut into multiple segments at a specific angle and then welded together to form a bend. Unlike traditional curved pipe bends, mitered bends allow for sharp directional changes in the pipeline, often used when space constraints or design requirements demand an angular change rather than a smooth curve. These bends are typically used when precise directional changes are necessary and where the space or radius available is limited.
Mitered bends are important because they allow engineers to achieve the required pipe direction without the need for large-radius bends, which can take up more space and material. Additionally, they are often more cost-effective and faster to manufacture compared to standard bends, making them a popular choice in tight or intricate piping systems. They are commonly used in industries such as oil and gas, chemical processing, power generation, and construction, where tight routing and flexibility are crucial. While mitered bends may not be as smooth as regular curved bends, their ability to save space and reduce costs makes them an essential option in many pipeline systems.
Ample Alloys is a leading manufacturer and supplier of high-quality mitered pipe bends, offering custom solutions for precise directional changes in piping systems. With expert craftsmanship and advanced welding techniques, we deliver durable, reliable bends tailored to meet industry standards. Whether for oil and gas, chemical, or power generation sectors, We ensures fast delivery and exceptional performance for every project.
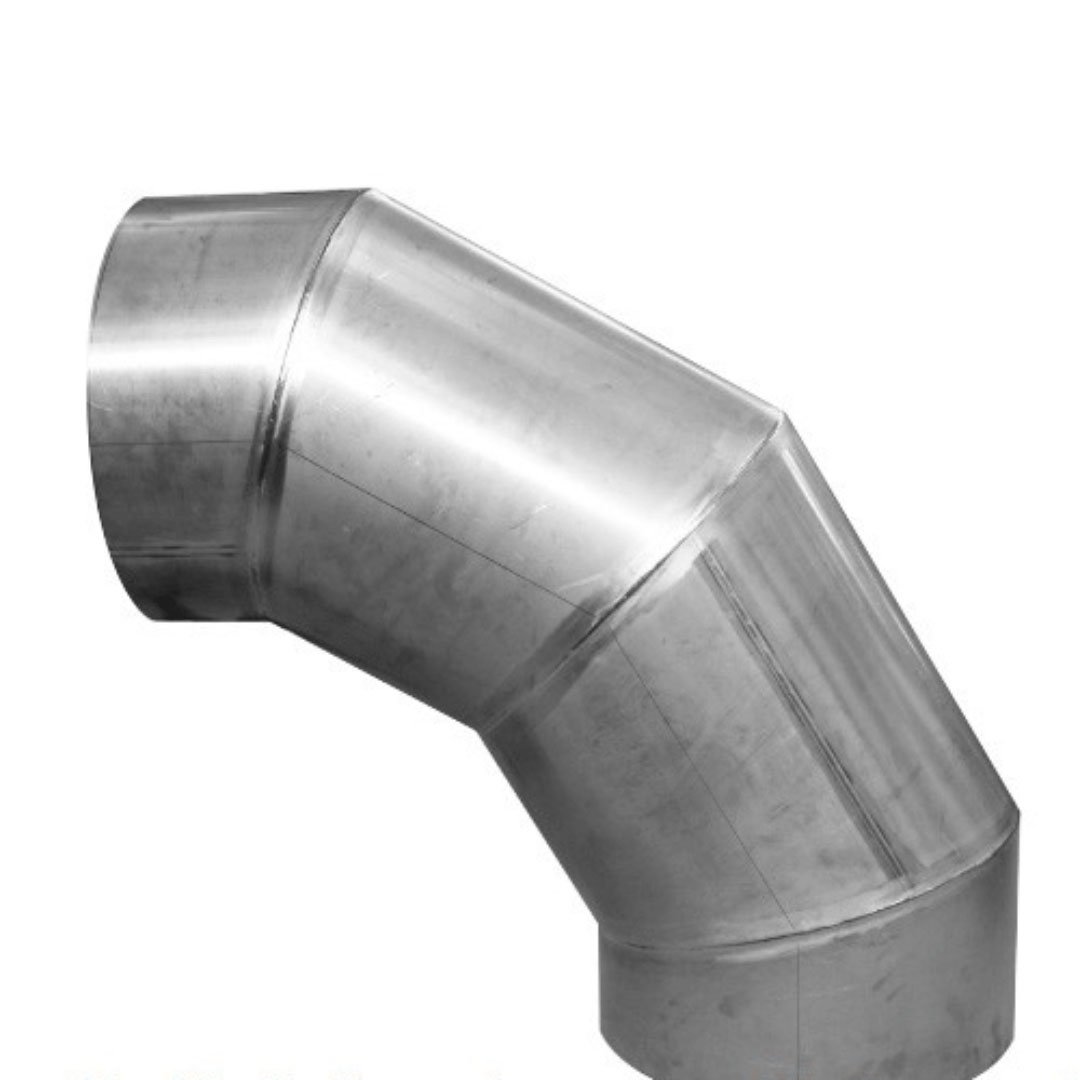
Mitered elbow bend, Mitered pipe fitting, 90-degree mitered bend, Mitered pipe angle, Mitered pipe bend welding, Mitered bend for pipelines, Mitered pipe bends for oil and gas & chemical industry, Custom mitered bends
Mitered elbow pipe bend Specifications
Size Range
1/8” NB TO 48” NB. (Seamless & 100% X-Ray Welded, Fabricated)
Wall Thickness
Sch 5s, 10s, 40s, 80s, 10, 20, 40, STD, 60, XS, 100, 120, 140, 160, Sch XXS
Stainless Steel
ASTM A403 WP 304, 304L, 304H, 316, 316L, 316H, 317, 317L, 321, 321H, 310, 310S, 347, 904L, etc.
Standards / Dimension
ASME B16.9, ASME B16.28, MSS SP-43, MSS SP-75, ASTM A234, ASTM A403, DIN 2605, 2615, 2616, 2617, 10253.
Type / Form
Seamless / ERW / Welded / Fabricated.
Alloy Steel
ASTM A234, WP1, WP5, WP9, WP11, WP22, WP91, etc.
Bending Radius
R=1D, 2D, 3D, 5D, 6D, 8D, 10D or Custom
Carbon Steel
ASTM A234, A420, MSS-SP-75, WPB, WPL3, WPL6, WPHY 42, WPHY 46, WPHY 52, WPHY 56, WPHY 60, WPHY 65, WPHY 70
Duplex & Super Duplex
ASTM A815 / A815M, UNS S31803 / 2205, UNS S32205, UNS S32101 / LDX 2101, UNS S32750 / 2507, UNS S32760, UNS S32550 / Ferralium 255.
ASME B16.9 Mitered Bends Dimensions
NOM. DIA |
A Min. | R Radius |
S Inches |
M |
---|---|---|---|---|
30 | 42w” | 45″ | 17p” | |
32 | 44s” | 48″ | 18s” | |
34 | 47r” | 51″ | 19f” | |
36 | 49f” | 54″ | 21w” | |
38 | 52i” | 57″ | 22r” | |
40 | 55w” | 60″ | 23i” | |
42 | 57s” | 63″ | 24p” | 8r” |
44 | 60r” | 66″ | 25s” | |
46 | 62f” | 69″ | 27″ | |
48 | 65i” | 72″ | 28i” | 9p” |
50 | 68w” | 75″ | 29r” | |
52 | 70s” | 78″ | 30i” | |
54 | 73r” | 81″ | 31p” | 10f” |
56 | 75f” | 84″ | 32f” | |
58 | 78i” | 87″ | 34″ | |
60 | 81w” | 90″ | 35w” | |
62 | 83s” | 93″ | 36y” | |
64 | 86y” | 96″ | 37i” | |
66 | 88f” | 99″ | 38p” | |
68 | 91i” | 102″ | 39f” | |
70 | 94w” | 105″ | 41″ | |
72 | 96s” | 108″ | 42r” | |
78 | 104i” | 117″ | 45s” | 15r” |
84 | 112y” | 126″ | 49i” | |
86 | 115″ | 129″ | 50y” |
Mitered pipe angle Tolerance
Parameter | Tolerance Range |
---|---|
Bend Radius | ± 5% of the specified radius |
Angle of Bend | ± 2° |
Wall Thickness | ± 10% |
Ovality | ± 3% of the nominal pipe diameter |
End-to-End Length | ± 1% |
Angle between segments (for segmented bends) | ± 1° - 2° for each segment |
Straight Length (before or after bend) | ± 5% of the nominal length |
Pipe Diameter | ± 1% |
Mitered pipe bend welding - Standard Specifications
These Mitered pipe bend specifications ensure that mitered pipe bends are designed, manufactured, and tested to meet the requirements of various industrial applications. Always confirm the detailed requirements for your specific project with the manufacturer to ensure compliance with standards and optimal performance.
- ASME Standards:
- ASME B16.9: Factory-Made Wrought Buttwelding Fittings.
- ASME B16.25: Buttwelding Ends (preparation of ends for welding).
- ASME Standards: Wrought Steel Buttwelding Short Radius Elbows and Returns.
- ASTM Standards:
- ASTM A234: Standard Specification for Piping Fittings of Wrought Carbon Steel and Alloy Steel for Moderate and High-Temperature Service.
- ASTM A403: Standard Specification for Wrought Austenitic Stainless Steel Piping Fittings.
- ASTM A815: Standard Specification for Wrought Ferritic, Ferritic/Austenitic (Duplex), and Martensitic Stainless Steel Piping Fittings.
- ASTM A860: Standard Specification for High-Strength Low-Alloy Welded Fittings (commonly used in pipelines with high strength requirements).
- API Standards:
- API 5L: Specification for Line Pipe (not directly for fittings but related to pipe material in oil and gas industries).
- API 6A: Specification for Wellhead and Christmas Tree Equipment (covers piping components but specific to high-pressure environments in oil fields).
- MSS (Manufacturers Standardization Society) Standards:
- MSS SP-43: Wrought and Fabricated Butt-Welding Fittings for Low-Pressure, Corrosion Resistant Applications (commonly used for stainless steel in low-pressure applications).
- MSS SP-75: Specification for High-Strength Wrought, Butt-Welding Fittings (used in oil and gas for high-strength requirements).
- MSS SP-79: Socket-Welding Reducer Inserts.
- MSS SP-83: Carbon Steel Pipe Unions, Socket Welding, and Threaded.
- DIN (Deutsches Institut für Normung) Standards (European):
- DIN 2605: Steel Elbows for Butt Welding (elbows dimensions and tolerances).
- DIN 2615: Tees for Butt Welding.
- DIN 2616: Reducers for Butt Welding.
- DIN 2617: Caps for Butt Welding.
- EN (European Norms) Standards:
- EN 10253-1: Butt-Welding Pipe Fittings Made of Non-Alloy and Alloy Steels.
- EN 10253-2: Butt-Welding Pipe Fittings with Specified Elevated Temperature Properties.
- EN 10253-3: Butt-Welding Pipe Fittings Made of Austenitic and Austenitic-Ferritic (Duplex) Stainless Steel.
- EN 10253-4: Butt-Welding Pipe Fittings for Low-Pressure Applications.
- JIS (Japanese Industrial Standards):
- JIS B2311: Steel Pipe Fittings for Butt-Welding.
- JIS B2312: Cast Iron Pipe Fittings for Butt-Welding.
- JIS B2313: Malleable Iron Pipe Fittings for Butt-Welding.
- ISO (International Standards Organization) Standards:
- ISO 5251: Specifications for Butt-Welding Ends for Steel Pipe Fittings (compatible with ISO pipes and equipment globally).
- ISO 15590: Petroleum and Natural Gas Industries — Induction Bends, Fittings, and Flanges for Pipeline Transportation Systems.
- BS (British Standards):
- BS 1640: Steel Butt-Welding Pipe Fittings for the Petroleum Industry.
- BS 3799: Forged Fittings, Screwed, and Socket-Welding for the Petroleum Industry
Why Ample Alloys for Mitered elbow bend!
When you choose Ample Alloys for your mitered bends, you're assured of superior craftsmanship, precision, and unparalleled service for all your piping system needs.
Accurate Testing Processes
Utilizing precise and accurate testing processes to ensure the highest quality and compliance with industry standards.
100% Satisfaction Guarantee
Experience peace of mind with our 100% Satisfaction Guarantee, ensuring top-quality products and services that exceed your expectations.
Highly Professional Staff
Backed by a team of highly professional staff, we deliver exceptional service and expertise to meet your industry needs.
Quality Control System
Ensuring excellence through a rigorous Quality Control System that meets the highest industry standards.
Mitered bends provide a more compact design compared to standard bends and can be used in applications where space constraints are a concern. They allow for sharper turns in the piping system, helping to optimize layout and flow.
The standard angles for mitered pipe bends are 30°, 45°, 60°, and 90°. However, custom angles can be designed to suit specific project requirements.
A mitered pipe bend consists of multiple segments welded together to form an angle, while a long-radius bend is a continuous curve with a specified radius. Mitered bends are more cost-effective for sharp changes in direction but may cause more turbulence in fluid flow compared to smooth-radius bends.