Stockist of Buttweld 8D Elbow Pipe Fittings | MSS-SP-43, ASME/ANSI B16.9, ANSI B16.28
An 8D bend is a type of buttweld elbow that has a centerline radius (the radius of the curvature) equal to 8 times the nominal pipe size (NPS). The "D" in the term stands for "diameter" or nominal pipe size. So, for example, for a 6-inch pipe, an 8D bend would have a centerline radius of 48 inches (6 inches × 8). This type of bend is often used in applications requiring a longer radius bend for smoother flow and reduced pressure drop compared to standard elbows.
The 8D elbow features a long, gradual curve, which is especially useful in piping systems that demand minimal turbulence and pressure loss. The longer radius of the 8D bend helps facilitate a smoother flow of liquids or gases, which reduces the chance of flow disruptions, making it ideal for sensitive processes. Because of the longer radius, 8D bends reduce the frictional losses typically seen in standard short-radius elbows, offering improved flow efficiency. Because of the longer radius, 8D bends reduce the frictional losses typically seen in standard short-radius elbows, offering improved flow efficiency.
Ample Alloys is a trusted manufacturer of 8D pipe bends, specializing in high-quality buttweld fittings that meet international standards. With a focus on precision and durability, our 8D bends are crafted to ensure smooth flow, reduced pressure drop, and enhanced system efficiency. Serving industries such as oil & gas, chemical, and power generation, we provide reliable and cost-effective solutions tailored to meet the specific needs of our clients. At Ample Alloys, we are committed to delivering exceptional products that guarantee long-term performance and superior value.
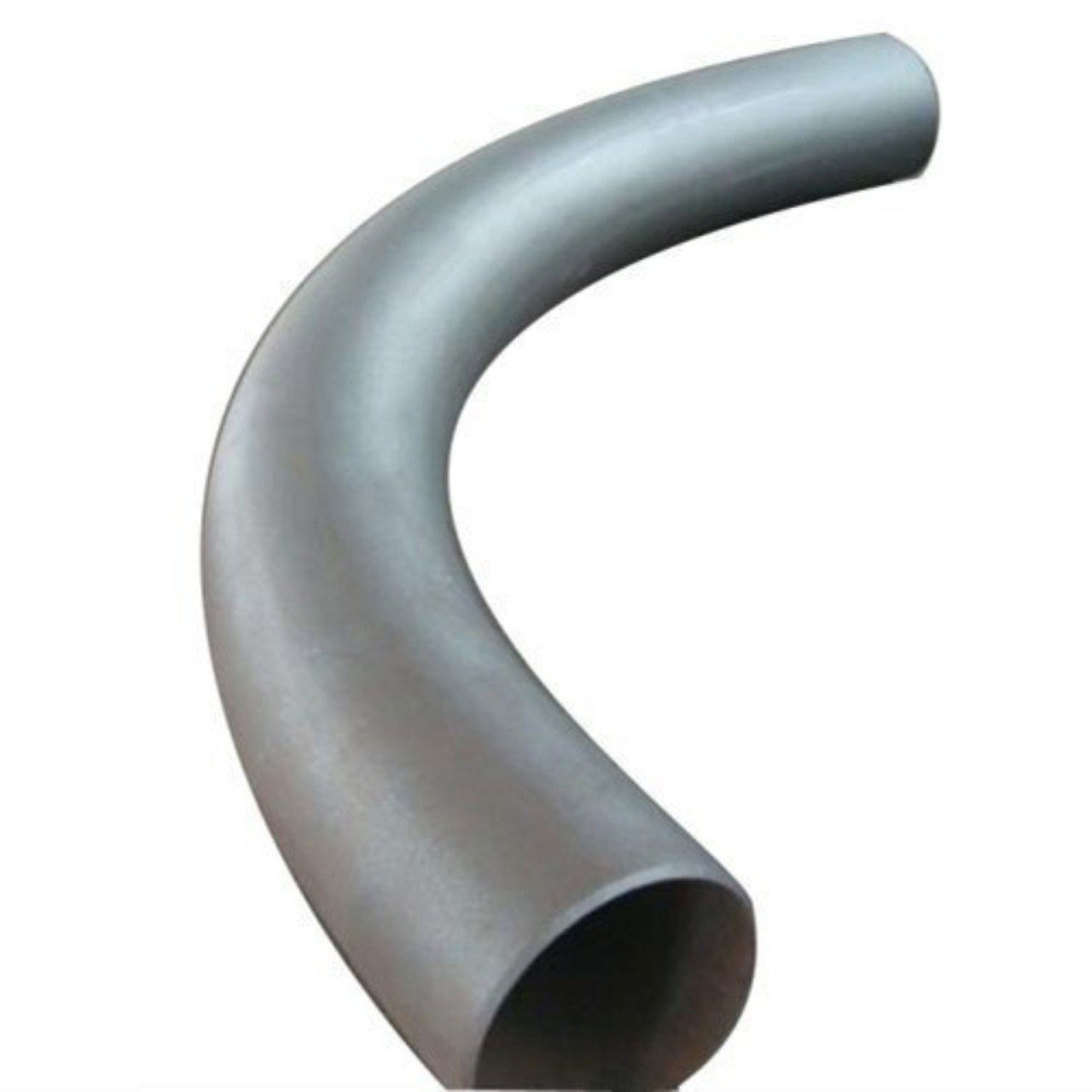
Long radius 8D elbow, 8D pipe fitting, 8D buttweld bend, 8D pipe bend suppliers, 8D radius elbow, High-quality 8D bend, 8D pipe bend for oil and gas, 8D bend for power generation, Stainless steel 8D bend, Alloy steel 8D bend, 8D bend for chemical plants, 8D long radius pipe bend.
8D Pipe Bend Specifications
Size Range
1/2” NB TO 36” NB. (Seamless up to 24”), (Welded 8” TO 36”)
Wall Thickness
Sch 5s, 10s, 40s, 80s, 10, 20, 40, STD, 60, XS, 100, 120, 140, 160, Sch XXS
Stainless Steel
ASTM A403 WP 304, 304L, 304H, 316, 316L, 316H, 317, 317L, 321, 321H, 310, 310S, 347, 904L, etc.
Standards / Dimension
ASME B16.9, ASME B16.28, MSS SP-43, MSS SP-75, ASTM A234, ASTM A403, DIN 2605, 2615, 2616, 2617, 10253.
Type / Form
Seamless, Welded, Fabricated / 8D Elbow, Bend.
Alloy Steel
ASTM A234, WP1, WP5, WP9, WP11, WP22, WP91, etc.
Bending Radius
R=1D, 2D, 3D, 5D, 6D, 8D, 10D or Custom
Carbon Steel
ASTM A234, A420, MSS-SP-75, WPB, WPL3, WPL6, WPHY 42, WPHY 46, WPHY 52, WPHY 56, WPHY 60, WPHY 65, WPHY 70
Duplex & Super Duplex
ASTM A815 / A815M, UNS S31803 / 2205, UNS S32205, UNS S32101 / LDX 2101, UNS S32750 / 2507, UNS S32760, UNS S32550 / Ferralium 255.
Butt weld 8D Elbow Dimensions
Standard pipe | Spec | . Bauart 5 | 2,5D | |
---|---|---|---|---|
DN | Diameter [ØD] | CLR | CLR | CLR |
20 | 26,9 | 110 | 67 | |
25 | 33,7 | 110 | 84 | |
32 | 42,4 | 110 | 106 | |
40 | 48,3 | 110 | 212 | |
50 | 60,3 | 125 | 151 | |
65 | 76,1 | 175 | 190 | |
80 | 88,9 | 205 | 222 | |
100 | 114,3 | 270 | 286 | |
125 | 139,7 | 330 | 350 | |
150 | 168,3 | 390 | 421 | |
200 | 219,1 | 510 | ||
250 | 273 | 650 | ||
300 | 323,9 | 775 | ||
350 | 355,6 | 850 | ||
400 | 406,4 | 970 | ||
500 | 508 | 1245 |
8D pipe bend angularity tolerance
ND | Max off angle | Max off plane |
---|---|---|
Q | P | |
1/2 a 4 | 1 | 2 |
5 a 8 | 2 | 4 |
10 a 12 | 3 | 5 |
14 a 16 | 3 | 7 |
18 a 24 | 4 | 10 |
26 a 30 | 5 | 10 |
32 a 42 | 5 | 13 |
44 a 48 | 5 | 20 |
Common Buttweld 8D Elbow Standards
Buttweld 8D Elbow Standards ensure that these long-radius elbows are manufactured and designed to meet industry requirements for performance, durability, and safety. Below are the key standards that typically apply to 8D elbows:
- ASME Standards:
- ASME B16.9: Factory-Made Wrought Buttwelding Fittings.
- ASME B16.25: Buttwelding Ends (preparation of ends for welding).
- ASME Standards: Wrought Steel Buttwelding Short Radius Elbows and Returns.
- ASTM Standards:
- ASTM A234: Standard Specification for Piping Fittings of Wrought Carbon Steel and Alloy Steel for Moderate and High-Temperature Service.
- ASTM A403: Standard Specification for Wrought Austenitic Stainless Steel Piping Fittings.
- ASTM A815: Standard Specification for Wrought Ferritic, Ferritic/Austenitic (Duplex), and Martensitic Stainless Steel Piping Fittings.
- ASTM A860: Standard Specification for High-Strength Low-Alloy Welded Fittings (commonly used in pipelines with high strength requirements).
- API Standards:
- API 5L: Specification for Line Pipe (not directly for fittings but related to pipe material in oil and gas industries).
- API 6A: Specification for Wellhead and Christmas Tree Equipment (covers piping components but specific to high-pressure environments in oil fields).
- MSS (Manufacturers Standardization Society) Standards:
- MSS SP-43: Wrought and Fabricated Butt-Welding Fittings for Low-Pressure, Corrosion Resistant Applications (commonly used for stainless steel in low-pressure applications).
- MSS SP-75: Specification for High-Strength Wrought, Butt-Welding Fittings (used in oil and gas for high-strength requirements).
- MSS SP-79: Socket-Welding Reducer Inserts.
- MSS SP-83: Carbon Steel Pipe Unions, Socket Welding, and Threaded.
- DIN (Deutsches Institut für Normung) Standards (European):
- DIN 2605: Steel Elbows for Butt Welding (elbows dimensions and tolerances).
- DIN 2615: Tees for Butt Welding.
- DIN 2616: Reducers for Butt Welding.
- DIN 2617: Caps for Butt Welding.
- EN (European Norms) Standards:
- EN 10253-1: Butt-Welding Pipe Fittings Made of Non-Alloy and Alloy Steels.
- EN 10253-2: Butt-Welding Pipe Fittings with Specified Elevated Temperature Properties.
- EN 10253-3: Butt-Welding Pipe Fittings Made of Austenitic and Austenitic-Ferritic (Duplex) Stainless Steel.
- EN 10253-4: Butt-Welding Pipe Fittings for Low-Pressure Applications.
- JIS (Japanese Industrial Standards):
- JIS B2311: Steel Pipe Fittings for Butt-Welding.
- JIS B2312: Cast Iron Pipe Fittings for Butt-Welding.
- JIS B2313: Malleable Iron Pipe Fittings for Butt-Welding.
- ISO (International Standards Organization) Standards:
- ISO 5251: Specifications for Butt-Welding Ends for Steel Pipe Fittings (compatible with ISO pipes and equipment globally).
- ISO 15590: Petroleum and Natural Gas Industries — Induction Bends, Fittings, and Flanges for Pipeline Transportation Systems.
- BS (British Standards):
- BS 1640: Steel Butt-Welding Pipe Fittings for the Petroleum Industry.
- BS 3799: Forged Fittings, Screwed, and Socket-Welding for the Petroleum Industry
Why Ample Alloys for 8D Bends!
Ample Alloys stands out as a trusted manufacturer and supplier of 8D bends, offering exceptional quality and performance for diverse industries.
Quality Control System
Ensuring excellence through a rigorous Quality Control System that meets the highest industry standards.
Premium Quality Products
manufacturing high-quality 3D bends with seamless construction and exceptional durability. Each product is engineered to meet stringent industry standards.
Custom Solutions
We offer tailored 3D bend solutions to meet unique project requirements, ensuring you receive the perfect fit for your pipeline systems.
Advanced Manufacturing Expertise
With state-of-the-art facilities and cutting-edge technology, we produce 3D bends that ensure precision, reliability, and superior performance in demanding applications.
8D elbows are widely used in industries such as oil & gas, petrochemical, chemical processing, power generation, and water treatment. They are ideal for applications where minimal flow disturbance and long-radius bends are required.
The primary difference between 8D and 5D elbows lies in the radius of the bend. An 8D elbow has a longer radius, making it suitable for applications where lower flow resistance and smoother directional changes are needed. 5D elbows, with a shorter radius, are typically used when space constraints require more compact bends.
- Reduced pressure drop due to smoother flow.
- Lower turbulence, improving the overall efficiency of the system.
- Suitable for high-pressure and high-temperature applications.
- Ideal for applications requiring minimal space between pipes.