Socket Weld & Threaded Fittings | ASME 16.11, MSS SP-79, 95, 83, 95, 97, BS 3799
Forged fittings are essential components used in piping systems to connect, divert, or control the flow of liquids, gases, or other substances. Manufactured through a forging process, these fittings are known for their superior mechanical properties, high strength, and durability, making them ideal for high-pressure and high-temperature applications.
Socket weld fittings are designed for pipes with smaller diameters (up to 4 inches) and are ideal for high-pressure systems. They ensure a smooth flow path and help prevent leakage, with common types including elbows, tees, couplings, and reducers.
Threaded fittings feature a screw-like connection for quick and easy assembly, making them suitable for low-pressure and non-critical applications. Popular types include threaded elbows, tees, caps, and unions.
high-pressure forged fittings are engineered to withstand extreme pressures and temperatures, making them essential in demanding industries such as oil & gas, petrochemicals, and power generation.
Forged pipe fittings are produced by heating a piece of metal and then shaping it under compressive forces. This process enhances the metal's strength and refines its grain structure, resulting in improved mechanical performance. The fittings are typically made from carbon steel, stainless steel, alloy steel, or exotic materials like nickel alloys, depending on the application's requirements.
Ample Alloys is a leading name in the manufacturing and supply of high-quality forged fittings, catering to a wide range of industries globally. With years of expertise and a commitment to precision engineering, the company has earned a reputation for delivering reliable and durable piping solutions for critical applications.
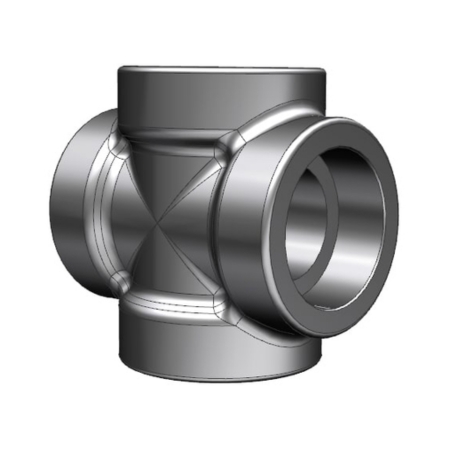
High-pressure forged fittings, Stainless steel forged fittings, Carbon steel forged fittings, Alloy steel forged fittings, Nickel alloy forged fittings, Durable forged steel fittings, API-compliant forged fittings, Corrosion-resistant forged pipe fittings
Forged Threaded Fittings Specifications
Size Range
1/8″~4″ (DN6~DN100)
Socket Weld Fittings Form
90° Elbow, 45° Elbow, Tee, Cross, Full Coupling, Half Coupling, Pipe Cap, Union, Reducer Insert, Boss, Branch Outlet, 90° Elbow Outlet, 45° Lateral Tee, Lateral Outlet, Branch Outlet Butt Weld, 90° Elbow Outlet Butt Weld, Lateral Outlet Butt Weld, Nipple Branch Outlet Butt Weld
Stainless Steel
ASTM A182 & ASME SA182 F 304, 304L, 304H, 316, 316L, 316H, 317, 317L, 321, 321H, 310, 310S, 347, 904L, etc.
Standards / Dimension
ASME 16.11, MSS SP-79, 83, 95, 97, BS 3799
Carbon Steel
ASTM A105, ASME SA105, A105N, ASTM A350 LF2, ASME SA350, ASTM A694, ASME SA694
Alloy Steel
ASTM A182 & ASME SA182 - F1, F5, F9, F11, F12, F22, F91
Pressure Class
2000LBS, 3000LBS, 6000LBS, 9000LBS
Threaded / Screwed Form
90° Elbow, 45° Elbow, Tee, Cross, Full Coupling, Half Coupling, Reducing Coupling, Pipe Cap, Hex Head Bushing, Hex Head Plug, Square Head Plug, Round Head Plug, Union, Hex Nipple, Street Elbow, Bull Plug, Boss, Swage Nipple, Pipe Nipple, Adapter, Union (Male x Female), Branch Outlet, 90° Elbow Outlet, 45° Lateral Tee, Lateral Outlet, Nipple Branch Outlet
Duplex & Super Duplex
ASTM A182 / ASME SA182 - S31803, S32205, 2205, S32750, S32760, 2507
ASME B16.11 Socket Weld Fittings Dimensions
Nom, Pipe Size | Sock, Bore Diameter B | Depth of Sock, Min | Wall Thickness Minimum | Bore Diameter of Fitting D | Centre to Bottom of Socket | Laying Lengths | Tolerances, ± | ||||||||||
---|---|---|---|---|---|---|---|---|---|---|---|---|---|---|---|---|---|
3000# | 6000# | 90º Elbow, Tee & Crosses | 45º Elbow | Couplings | Half Couplings | ||||||||||||
A | A | E | F | A | E | F | |||||||||||
Sock, C | Body G | Sock C | Body G | 3000# | 6000# | 3000# | 6000# | 3000# | 6000# | ||||||||
1/8” | .420
.430 |
3/8 | .125 | .095 | .135 | .124 | .254
.284 |
.141 | 7/16 | 7/16 | 5/16 | 5/16 | 1/4 | 5/8 | .03 | .06 | .03 |
1/4 | .555
.565 |
3/8 | .130 | .119 | .158 | .145 | .349
.379 |
.235 | 7/16 | 17/32 | 5/16 | 5/16 | 1/4 | 5/8 | .03 | .06 | .03 |
3/8 | .690
.700 |
3/8 | .138 | .126 | .172 | .158 | .478
.508 |
.344 | 17/32 | 5/8 | 5/16 | 7/16 | 1/4 | 11/16 | .06 | .12 | .06 |
1/2 | .855
.865 |
3/8 | .161 | .147 | .204 | .188 | .607
.637 |
.451 | 5/8 | 3/4 | 7/16 | 1/2 | 3/8 | 7/8 | .06 | .12 | .06 |
3/4 | 1.065
1.075 |
1/2 | .168 | .154 | .238 | .219 | .809
.839 |
.599 | 3/4 | 7/8 | 1/2 | 9/16 | 3/8 | 15/16 | .06 | .12 | .06 |
1 | 1.330
1.340 |
1/2 | .196 | .179 | .273 | .250 | 1.034
1.064 |
.800 | 7/8 | 1-1/16 | 9/16 | 11/16 | 1/2 | 1-1/8 | .08 | .16 | .08 |
1-1/4 | 1.675
1.685 |
1/2 | .208 | .191 | .273 | .250 | 1.365
1.395 |
1.145 | 1-1/16 | 1-1/4 | 11/16 | 13/16 | 1/2 | 1-3/16 | .08 | .16 | .08 |
1-1/2 | 1.915
1.925 |
1/2 | .218 | .200 | .307 | .281 | 1.595
1.625 |
1.323 | 1-1/4 | 1-1/2 | 13/16 | 1 | 1/2 | 1-1/4 | .08 | .16 | .08 |
2 | 2.406
2.416 |
5/8 | .238 | .218 | .374 | .344 | 2.052
2.082 |
1.674 | 1-1/2 | 1-5/8 | 1 | 1-1/8 | 3/4 | 1-5/8 | .08 | .16 | .08 |
2-1/2 | 2.906
2.921 |
5/8 | .301 | .276 | .375 | 2.439
2.499 |
1-5/8 | 1-1/8 | 3/4 | 1-11/16 | .10 | .20 | .10 | ||||
3 | 3.535
3.550 |
5/8 | .327 | .300 | .438 | 3.038
3.098 |
2-1/4 | 1-1/4 | 3/4 | 1-3/4 | .10 | .20 | .10 | ||||
4 | 4.545
4.560 |
3/4 | .368 | .337 | .531 | 3.996
4.055 |
2-5/8 | 1-5/8 | 3/4 | 1-7/8 | .10 | .20 | .10 |
Nominal Pipe Size | Centre to End Elbows, Tee, Crosses A | Centre to End 45º Elbows C | Outside Diameter of Band H | Minimum Wall Thickness G | Lengths of Thread Min | |||||||||
---|---|---|---|---|---|---|---|---|---|---|---|---|---|---|
2000# | 3000# | 6000# | 2000# | 3000# | 6000# | 2000# | 3000# | 6000# | 2000# | 3000# | 6000# | B | L2 | |
1/8 | 13/16 | 13/16 | 31/32 | 11/16 | 11/16 | 3/4 | 7/8 | 7/8 | 1 | .125 | .125 | .250 | .25 | .2639 |
1/4 | 13/16 | 31/32 | 1-1/8 | 11/16 | 3/4 | 7/8 | 7/8 | 1 | 1-5/16 | .125 | .130 | .260 | .32 | .4018 |
3/8 | 3/32 | 1-1/8 | 1-5/16 | 3/4 | 7/8 | 1 | 1 | 1-5/16 | 1-1/2 | .125 | .138 | .275 | .36 | .4078 |
1/2 | 1-1/8 | 1-5/16 | 1-1/2 | 7/8 | 1 | 1-1/8 | 1-5/16 | 1-1/2 | 1-13/16 | .125 | .161 | .321 | .43 | .5337 |
3/4 | 1-5/16 | 1-1/2 | 1-3/4 | 1 | 1-1/8 | 1-5/16 | 1-1/2 | 1-13/16 | 2-3/16 | .123 | .168 | .336 | .50 | .5457 |
1 | 1-1/2 | 1-3/4 | 2 | 1-1/8 | 1-5/16 | 1-3/8 | 1-13/16 | 2-3/16 | 2-7/16 | .145 | .196 | .391 | .58 | .6828 |
1-1/4 | 1-3/4 | 2 | 2-3/8 | 1-15/16 | 1-3/8 | 1-11/16 | 2-3/16 | 2-7/16 | 2-31/32 | .153 | .208 | .417 | .67 | .7068 |
1-1/2 | 2 | 2-3/8 | 2-1/2 | 1-3/8 | 1-11/16 | 1-23/32 | 2-7/16 | 2-31/32 | 3-5/16 | .158 | .218 | .436 | .70 | .7235 |
2 | 2-3/8 | 2-1/2 | 3-3/4 | 1-11/16 | 1-23/32 | 2-1/16 | 2-31/32 | 3-5/16 | 4 | .168 | .238 | .476 | .75 | .7565 |
2-1/2 | 3 | 3-1/4 | 3-3/4 | 2-1/16 | 2-1/16 | 2-1/2 | 3-5/8 | 4 | 4 | .221 | .301 | .602 | .932 | 1.138 |
3 | 3-3/8 | 3-3/4 | 4-3/16 | 2-1/2 | 2-1/2 | 3-1/8 | 4-5/16 | 4-3/4 | 4-3/4 | .236 | .327 | .655 | 1.016 | 1.200 |
4 | 3-3/16 | 4-1/2 | 4-1/2 | 3-1/8 | 3-1/8 | 3-1/8 | 5-3/4 | 5 | 6 | .258 | .368 | .735 | 1.094 | 1.300 |
ASME B16.11 Threaded Fittings Dimensions
Nominal Pipe Size | End to End Couplings W | End to End Caps H |
Outside Diameter D |
End Wall Thickness G Min |
Length of Thead Min |
||||
---|---|---|---|---|---|---|---|---|---|
3000# & 6000# |
3000# | 6000# | 3000# | 6000# | 3000# | 6000# | B | L2 | |
1/8 | 1-1/4 | 3/4 | 5/8 | 7/8 | 3/16 | .25 | .2639 | ||
1/4 | 1-3/8 | 1 | 1-1/16 | 3/4 | 1 | 3/16 | 1/4 | .32 | .4018 |
3/8 | 1-1/2 | 1 | 1-1/16 | 7/8 | 1-1/4 | 3/16 | 1/4 | .36 | .4078 |
1/2 | 1-7/8 | 1-1/4 | 1-5/16 | 1-1/8 | 1-1/2 | 1/4 | 5/16 | .43 | .5337 |
3/4 | 2 | 1-7/16 | 1-1/2 | 1-3/8 | 1-3/4 | 1/4 | 5/16 | .50 | .5457 |
1 | 2-3/8 | 1-5/8 | 1-11/16 | 1-3/4 | 2-1/4 | 3/8 | 7/16 | .58 | .6828 |
1-1/4 | 2-5/8 | 1-3/4 | 1-13/16 | 2-1/4 | 2-1/2 | 3/8 | 7/16 | .67 | .7068 |
1-1/2 | 3-1/8 | 1-3/4 | 1-7/8 | 2-1/2 | 3 | 7/16 | 1/2 | .70 | .7235 |
2 | 3-3/8 | 1-7/8 | 2 | 3 | 3-5/8 | 1/2 | 5/8 | .75 | .7565 |
2-1/2 | 3-5/8 | 2-3/8 | 2-1/2 | 3-5/8 | 4-1/4 | 5/8 | 3/4 | .932 | 1.138 |
3 | 4-1/4 | 2-9/16 | 2-11/16 | 4-1/4 | 5 | 3/4 | 7/8 | 1.016 | 1.200 |
4 | 4-3/4 | 2-11/16 | 2-15/16 | 5-1/2 | 6-1/4 | 7/8 | 1-1/8 | 1.094 | 1.300 |
Nominal Pipe Size | Thead
Length (min) |
Plugs Square Head | Plugs Round Head | Hexagon Plugs & Bushings |
||||
---|---|---|---|---|---|---|---|---|
Height of Square (min) B |
Width Flats (min) C |
Nominal Diameter of Head
E |
Length (min) D |
Width Flats (min) F |
Hexagon Height min | |||
Bushings G | Plug H |
|||||||
1/8 | 3/8 | 1/4 | 9/32 | 13/32 | 1-3/8 | 7/16 | – | 1/4 |
1/4 | 7/16 | 1/4 | 3/8 | 17/32 | 1-5/8 | 5/8 | 1/8 | 1/4 |
3/8 | 1/2 | 5/16 | 7/16 | 11/16 | 1-5/8 | 11/16 | 5/32 | 5/16 |
1/2 | 9/16 | 3/8 | 9/16 | 27/32 | 1-3/4 | 7/8 | 3/16 | 5/16 |
3/4 | 5/8 | 7/16 | 5/8 | 1-1/16 | 1-3/4 | 1-1/16 | 7/32 | 3/8 |
1 | 3/4 | 1/2 | 13/16 | 1-5/16 | 2 | 1-3/8 | 1/4 | 3/8 |
1-1/4 | 13/16 | 9/16 | 15/16 | 1-11/16 | 2 | 1-3/4 | 9/32 | 9/16 |
1-1/2 | 13/16 | 5/8 | 1-1/8 | 1-29/32 | 2 | 2 | 5/16 | 5/8 |
2 | 7/8 | 11/16 | 1-5/16 | 2-3/8 | 2-1/2 | 2-1/2 | 11/32 | 11/16 |
2-1/2 | 1-1/16 | 3/4 | 1-1/2 | 2-7/8 | 2-3/4 | 3 | 3/8 | 3/4 |
3 | 1-1/8 | 13/16 | 1-11/16 | 3-1/2 | 2-3/4 | 3-1/2 | 13/32 | 13/16 |
3-1/2 | 1-3/16 | 7/8 | 1-7/8 | 4 | 3 | 4-1/8 | 7/16 | 7/8 |
4 | 1-1/4 | 1-1/4 | 2-1/2 | 4-1/2 | 3 | 4-5/8 | 1/2 | 1-1/4 |
Forged Pipe Fittings Standards
Forged fittings are manufactured and tested according to internationally recognized standards to ensure safety, quality, and compatibility across various industries. Below are the key standards associated with forged pipe fittings:
- ASME Standards (American Standards):
- ASME B16.11: Covers forged fittings such as socket weld and threaded fittings for high-pressure applications.
- ASTM A105: Specifies carbon steel forgings for piping components.
- ASTM A182: Standard for forged or rolled alloy and stainless steel materials for high-temperature service.
- ASTM A350: Covers low-alloy and carbon steel forgings for low-temperature applications.
- MSS-SP-79: Socket weld fittings with enhanced dimensions and tolerances.
- MSS-SP-83: Threaded and socket weld unions for the petroleum industry.
- EN (European Standards):
- EN 10222: Forged steel fittings for pressure purposes.
- EN 10241: Steel threaded pipe fittings for the European market.
- EN ISO 17292: Specifications for fittings used in valve systems.
- JIS (Japanese Standards) :
- JIS B2316: Covers forged steel pipe fittings such as elbows, tees, and reducers.
- JIS G3454/G3455: Pressure-resistant pipe materials for fittings.
- International Standards:
- DIN 2605: German standard for forged fittings, particularly elbows.
- BS 3799: British standard for forged pipe fittings in threaded and socket weld types.
- GOST 17375: Russian standard for forged fittings used in high-pressure piping.
- Common Testing Standards:
- ASME B31.3: Testing requirements for process piping.
- NACE MR0175/ISO 15156: Compliance for materials in sour gas environments.
- API 598: Valve and fitting inspection standards.
Why Ample Alloys For Forged Fittings!
Ample Alloys is a leading manufacturer and supplier of high-quality forged fittings, trusted globally for its commitment to excellence, precision, and customer satisfaction.
Exceptional Quality Assurance
Comprehensive quality control processes, including rigorous testing like hydrostatic, radiographic, and NDT inspections.
Customization Expertise
Capability to produce custom forged fittings to match exact specifications. Solutions tailored for unique industrial requirements, material grades, and dimensional tolerances.
Global Reputation
Proven track record of supplying forged fittings to clients across Asia, Europe, the Middle East, and beyond.
Competitive Pricing and Timely Delivery
Affordable pricing structures without compromising on quality. An efficient supply chain ensures on-time delivery, even for urgent orders.
- Socket Weld Fittings: Designed for welding to ensure a strong, leak-proof joint, ideal for high-pressure systems.
- Threaded Fittings: Feature a screw-like connection for easy assembly and disassembly, suitable for low-pressure applications.
- Oil & Gas
- Petrochemicals
- Power Generation
- Pharmaceuticals
- Water Treatment
- Construction
Forged fittings are made by heating steel and shaping it into the desired form using a forging press or hammer. This process increases the strength and durability of the fittings.