Buttweld Hot Induction Bends Supplier & Exporter| ASME/ANSI B16.9, ANSI B16.28
A hot induction bend is a type of pipe bend that is formed using a specialized process known as induction bending. In this process, the pipe is heated using an induction coil to a high temperature, making it malleable and easier to bend without compromising the material's integrity. Once the pipe reaches the required temperature, it is bent to the desired angle and radius using hydraulic pressure. This method allows for precise, smooth bends without causing distortions or thinning of the pipe wall, which can be a concern with traditional bending techniques.
Hot induction bending is primarily used for larger diameter pipes, especially in high-stress applications where durability and reliability are crucial. Industries such as oil and gas, power generation, and petrochemical rely on this method due to its ability to produce strong, consistent bends that can withstand high pressures and temperatures. The key advantages of hot induction bending include minimal distortion, reduced material wastage, and the ability to create complex bends without compromising strength. Additionally, it ensures a smooth inner surface, reducing the chances of flow restrictions and pressure loss in the system.
At Ample Alloys, we specialize in manufacturing high-quality hot induction bends tailored to meet the demanding needs of various industries. Our hot induction bending process ensures that every bend is crafted with precision, strength, and durability, making it ideal for applications that require seamless fluid flow and minimal pressure loss. We use state-of-the-art induction heating technology to carefully heat the pipes to the optimal temperature, allowing us to achieve precise bends without compromising material integrity.
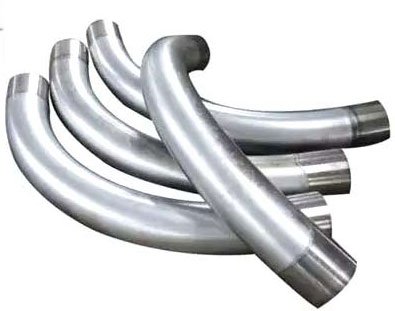
Induction bends for pipes, Custom hot induction bends, High-quality hot induction bends, Hot induction bends for oil and gas, Large diameter hot induction bends, Hot bend pipe fittings, Seamless hot induction bends, Induction bending for piping systems, Induction bend radius, Precision hot induction bends
ASME B16.9 Hot Induction Bends Specifications
Size Range
1/8” NB TO 48” NB. (Seamless & 100% X-Ray Welded, Fabricated)
Wall Thickness
Sch 5s, 10s, 40s, 80s, 10, 20, 40, STD, 60, XS, 100, 120, 140, 160, Sch XXS
Stainless Steel
ASTM A403 WP 304, 304L, 304H, 316, 316L, 316H, 317, 317L, 321, 321H, 310, 310S, 347, 904L, etc.
Standards / Dimension
ASME B16.9, ASME B16.28, MSS SP-43, MSS SP-75, ASTM A234, ASTM A403, DIN 2605, 2615, 2616, 2617, 10253.
Type / Form
Seamless / ERW / Welded / Fabricated.
Alloy Steel
ASTM A234, WP1, WP5, WP9, WP11, WP22, WP91, etc.
Bending Radius
R=1D, 2D, 3D, 5D, 6D, 8D, 10D or Custom
Carbon Steel
ASTM A234, A420, MSS-SP-75, WPB, WPL3, WPL6, WPHY 42, WPHY 46, WPHY 52, WPHY 56, WPHY 60, WPHY 65, WPHY 70
Duplex & Super Duplex
ASTM A815 / A815M, UNS S31803 / 2205, UNS S32205, UNS S32101 / LDX 2101, UNS S32750 / 2507, UNS S32760, UNS S32550 / Ferralium 255.
ANSI B16.9 Hot Induction Bends Dimensions
Pipe Nominal Diameter | Outside Diameter (OD) | Wall Thickness (WT) | Bend Radius (R) | Bend Angle | Push Force (P) | Bend Roll Force (Fb) |
---|---|---|---|---|---|---|
DN 50 (2") | 60.3 mm | 3.91 mm | 1.5D, 3D, 5D | 45°, 90° | 500 - 1000 N | 300 - 700 N |
DN 65 (2.5") | 73.0 mm | 5.16 mm | 1.5D, 3D, 5D | 45°, 90° | 700 - 1400 N | 400 - 900 N |
DN 80 (3") | 88.9 mm | 5.49 mm | 1.5D, 3D, 5D | 45°, 90° | 1000 - 2000 N | 500 - 1100 N |
DN 100 (4") | 114.3 mm | 6.02 mm | 1.5D, 3D, 5D | 45°, 90° | 1500 - 3000 N | 700 - 1500 N |
DN 150 (6") | 168.3 mm | 7.11 mm | 1.5D, 3D, 5D | 45°, 90° | 2500 - 5000 N | 1000 - 2000 N |
DN 200 (8") | 219.1 mm | 8.18 mm | 1.5D, 3D, 5D | 45°, 90° | 4000 - 8000 N | 1500 - 3000 N |
DN 250 (10") | 273.0 mm | 9.27 mm | 1.5D, 3D, 5D | 45°, 90° | 6000 - 12000 N | 2000 - 4000 N |
DN 300 (12") | 323.9 mm | 9.53 mm | 1.5D, 3D, 5D | 45°, 90° | 8000 - 15000 N | 3000 - 6000 N |
DN 350 (14") | 355.6 mm | 9.53 mm | 1.5D, 3D, 5D | 45°, 90° | 10000 - 20000 N | 3500 - 7000 N |
DN 400 (16") | 406.4 mm | 10.31 mm | 1.5D, 3D, 5D | 45°, 90° | 12000 - 25000 N | 4000 - 8000 N |
DN 450 (18") | 457.2 mm | 10.31 mm | 1.5D, 3D, 5D | 45°, 90° | 15000 - 30000 N | 4500 - 9000 N |
DN 500 (20") | 508.0 mm | 11.13 mm | 1.5D, 3D, 5D | 45°, 90° | 18000 - 36000 N | 5000 - 10000 N |
DN 600 (24") | 609.6 mm | 12.70 mm | 1.5D, 3D, 5D | 45°, 90° | 24000 - 48000 N | 6000 - 12000 N |
Tolerance of Hot Induction Pipe Bends
Dimension | Tolerance |
---|---|
Bend Angle | ± 1° to ± 2° |
Bend Radius | ± 2% of the nominal radius |
Wall Thickness | ± 5% |
Outside Diameter | ± 2% |
Length of Bend (L) | ± 3% |
Pipe End Squareness | ± 1° |
Bend Length (perpendicular to the centerline) | ± 2% to ± 5% |
Wall Thickness Deviation (after bending) | ± 5% of original thickness |
Ovality (Deformation of the cross-section) | ≤ 5% of the pipe diameter |
Axial Deviation | ± 2% |
Seamless hot induction bends - Standard Specifications
hot induction bends are manufactured using the induction bending process, which involves heating a pipe to a high temperature and then bending it into the desired angle and radius. These bends are designed for high-performance applications, providing strength, flexibility, and durability. Below are the standard specifications for hot induction bends:
- ASME Standards:
- ASME B16.9: Factory-Made Wrought Buttwelding Fittings.
- ASME B16.25: Buttwelding Ends (preparation of ends for welding).
- ASME Standards: Wrought Steel Buttwelding Short Radius Elbows and Returns.
- ASTM Standards:
- ASTM A234: Standard Specification for Piping Fittings of Wrought Carbon Steel and Alloy Steel for Moderate and High-Temperature Service.
- ASTM A403: Standard Specification for Wrought Austenitic Stainless Steel Piping Fittings.
- ASTM A815: Standard Specification for Wrought Ferritic, Ferritic/Austenitic (Duplex), and Martensitic Stainless Steel Piping Fittings.
- ASTM A860: Standard Specification for High-Strength Low-Alloy Welded Fittings (commonly used in pipelines with high strength requirements).
- API Standards:
- API 5L: Specification for Line Pipe (not directly for fittings but related to pipe material in oil and gas industries).
- API 6A: Specification for Wellhead and Christmas Tree Equipment (covers piping components but specific to high-pressure environments in oil fields).
- MSS (Manufacturers Standardization Society) Standards:
- MSS SP-43: Wrought and Fabricated Butt-Welding Fittings for Low-Pressure, Corrosion Resistant Applications (commonly used for stainless steel in low-pressure applications).
- MSS SP-75: Specification for High-Strength Wrought, Butt-Welding Fittings (used in oil and gas for high-strength requirements).
- MSS SP-79: Socket-Welding Reducer Inserts.
- MSS SP-83: Carbon Steel Pipe Unions, Socket Welding, and Threaded.
- DIN (Deutsches Institut für Normung) Standards (European):
- DIN 2605: Steel Elbows for Butt Welding (elbows dimensions and tolerances).
- DIN 2615: Tees for Butt Welding.
- DIN 2616: Reducers for Butt Welding.
- DIN 2617: Caps for Butt Welding.
- EN (European Norms) Standards:
- EN 10253-1: Butt-Welding Pipe Fittings Made of Non-Alloy and Alloy Steels.
- EN 10253-2: Butt-Welding Pipe Fittings with Specified Elevated Temperature Properties.
- EN 10253-3: Butt-Welding Pipe Fittings Made of Austenitic and Austenitic-Ferritic (Duplex) Stainless Steel.
- EN 10253-4: Butt-Welding Pipe Fittings for Low-Pressure Applications.
- JIS (Japanese Industrial Standards):
- JIS B2311: Steel Pipe Fittings for Butt-Welding.
- JIS B2312: Cast Iron Pipe Fittings for Butt-Welding.
- JIS B2313: Malleable Iron Pipe Fittings for Butt-Welding.
- ISO (International Standards Organization) Standards:
- ISO 5251: Specifications for Butt-Welding Ends for Steel Pipe Fittings (compatible with ISO pipes and equipment globally).
- ISO 15590: Petroleum and Natural Gas Industries — Induction Bends, Fittings, and Flanges for Pipeline Transportation Systems.
- BS (British Standards):
- BS 1640: Steel Butt-Welding Pipe Fittings for the Petroleum Industry.
- BS 3799: Forged Fittings, Screwed, and Socket-Welding for the Petroleum Industry
Why Ample Alloys for Hot Induction Pipe Bend!
Choose Ample Alloys for your hot induction pipe bends and experience exceptional quality, custom solutions, and reliable service that ensures the long-term performance and success of your piping systems.
Highly Professional Staff
Backed by a team of highly professional staff, we deliver exceptional service and expertise to meet your industry needs.
100% Satisfaction Guarantee
Experience peace of mind with our 100% Satisfaction Guarantee, ensuring top-quality products and services that exceed your expectations.
Quality Control System
Ensuring excellence through a rigorous Quality Control System that meets the highest industry standards.
Accurate Testing Processes
Utilizing precise and accurate testing processes to ensure the highest quality and compliance with industry standards.
- Improved Flow Efficiency: The smooth bends reduce turbulence and pressure loss, optimizing flow.
- Seamless Construction: Unlike welded bends, there are no joints or welds, reducing the risk of leakage.
- Customizable: Available in various sizes, bend radii, and angles to meet specific project requirements.
- Stronger and More Durable: Seamless design provides higher strength and durability, especially under high-pressure conditions.
1.5D, 2D, 3D, etc. Where D is the nominal diameter of the pipe. Custom radii are also available based on project needs.
- Seamless vs. Welded: Hot induction bends are seamless, while welded bends have a welded joint, which can be prone to defects.
- Strength and Durability: Hot induction bends are stronger and more durable, making them suitable for high-stress and high-pressure applications.
- Flow Efficiency: Hot induction bends provide smoother flow due to their seamless construction.